Know-how and expertise cannot be decreed: they have to be earned and acquired in the field. They are also accompanied by investments and technical choices that shape the ambition and objectives to be achieved. Geplast’s know-how and expertise are illustrated by the presence in its production unit of a tooling and equipment workshop at the cutting edge of innovation, a design office, a high-performance quality department, etc.
More than 20 years’ experience in the design and extrusion of profiles has enabled Geplast to develop comprehensive product ranges for a wide range of markets: construction, outdoor, marine, agriculture, light housing, etc. Geplast’s development resources, the quality of its teams and the expertise it has acquired mean that it can be a force to be reckoned with when it comes to tailor-made profiles for manufacturers and industrialists.
Our expertises
1 – Conception of the specifications
The technical and innovation department is made up of specialists who support customers in drawing up their specifications and defining the product for any sector of activity.
These studies take into account all the technical and regulatory constraints, while respecting “eco-design” The result is high-performance and efficient solutions for all types of project. Geplast has the industrial resources to help you make the right decisions. Equipped with a 3D printer and high-performance IT tools, Geplast makes your future product a reality.
2 – Creation of tooling
The design office, staffed by experts, is equipped with CAD/CAM tools to design toolings and moulds.
By investing in modern equipment such as a machining centre, wire EDM machines, a profiling machine…, Geplast integrates technical developments to maintain a high level of performance. Testing and fine-tuning are carried out in-house, in real production situations.
3 – Profile extrusion
Geplast has 30 extrusion lines and a profiling machine.
The machines can produce single, dual or tri-material profiles from 15 to 4,000 g. Divided up by field of activity, the first production area is dedicated to the extrusion of our ranges of profiles for joinery, roller shutters, fencing and gates. The second workshop is dedicated to thermal breaks or any other complex specific profile requiring different operations. Finishing services are offered, such as the fitting of protective film, adhesive removal, drilling, in-line punching, etc. The third workshop is reserved for the aluminium bioclimatic® roller shutter slat profiling machine. This 50-metre-long machine can cut up to 350 6-ml bars per hour.
4 – Finishing
With two in-house filming lines, Geplast is expanding its range of decors. More than 70 films are held in stock to meet the specific regional requirements and architectural trends of the market.
Since 2016, Geplast has acquired expertise in aluminium cladding (profiles covered with aluminium foil).
Geplast has its own bending workshop, giving it specific, complementary expertise and the ability to create shapes on its profiles.
5 – Logistics
Geplast provides its customers with the benefit of its logistical strength, with regular deliveries throughout France and a 15,000 m² storage platform. These facilities guarantee a high level of service, regardless of the delivery location.
Whether it’s specific or standard packaging, the logistics department can respond to any request for order planning and delivery tracking.
6 – Recycling
Always mindful of the need to protect the environment, Geplast recycles all its manufacturing waste in order to reduce its environmental footprint. This approach includes using lead-free vinyl compounds in the manufacture of profiles (the new formulas are calcium-zinc stabilised), recycling waste by giving new life to materials, solvent-free inkjet marking and the use of recycled cardboard.
As part of its efforts to minimise the environmental impact of joinery, Geplast has made a commitment to UFME to improve the recycling of its products at the end of their life.
Dans le cadre de ses actions visant à minimiser l’impact environnemental des menuiseries, Geplast s’est engagée auprès de l’UFME pour améliorer le recyclage de ses produits en fin de vie.
Materials focus
Geplast uses a variety of materials to make its fences, gates, swing shutters, roller shutters, thermal breaks and special tailor-made profiles, with a constant eye to efficiency, modernity, practicality and respect for the environment. Focus on these different materials…
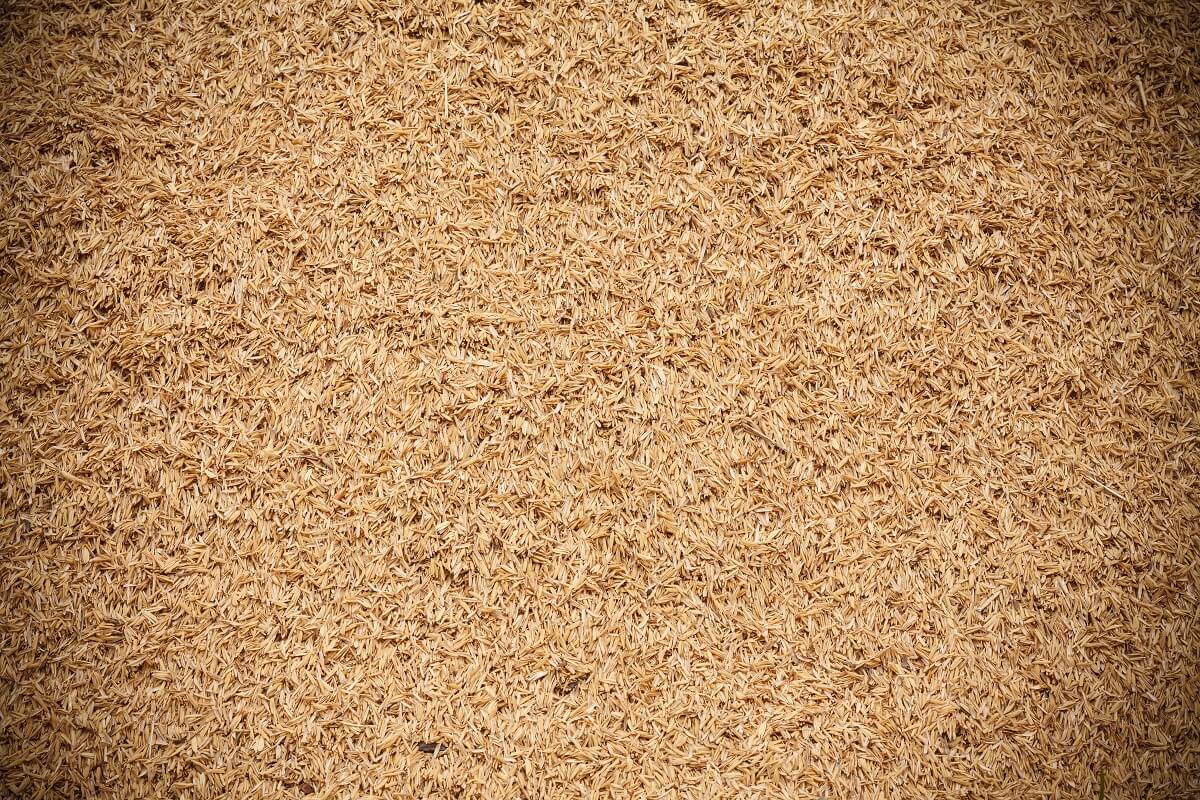
THE LORYZA®
Loryza® is a bio-sourced material made essentially from rice husks, a hitherto little-used food residue that requires no specific cultivation or deforestation. It is a virtually inexhaustible agricultural resource that is available all over the world.
The mixture of rice hulls (60%) and PVC has created an extremely resistant and durable material. Loryza® has all the advantages of wood, without the constraints.
In addition to its warm appearance and pleasant, splinter-free feel, the finished product won’t crack or splinter, won’t slip and, above all, is rot-proof.
The ultimate advantage? Loryza® is 100% recyclable and comes with a 15-year guarantee.
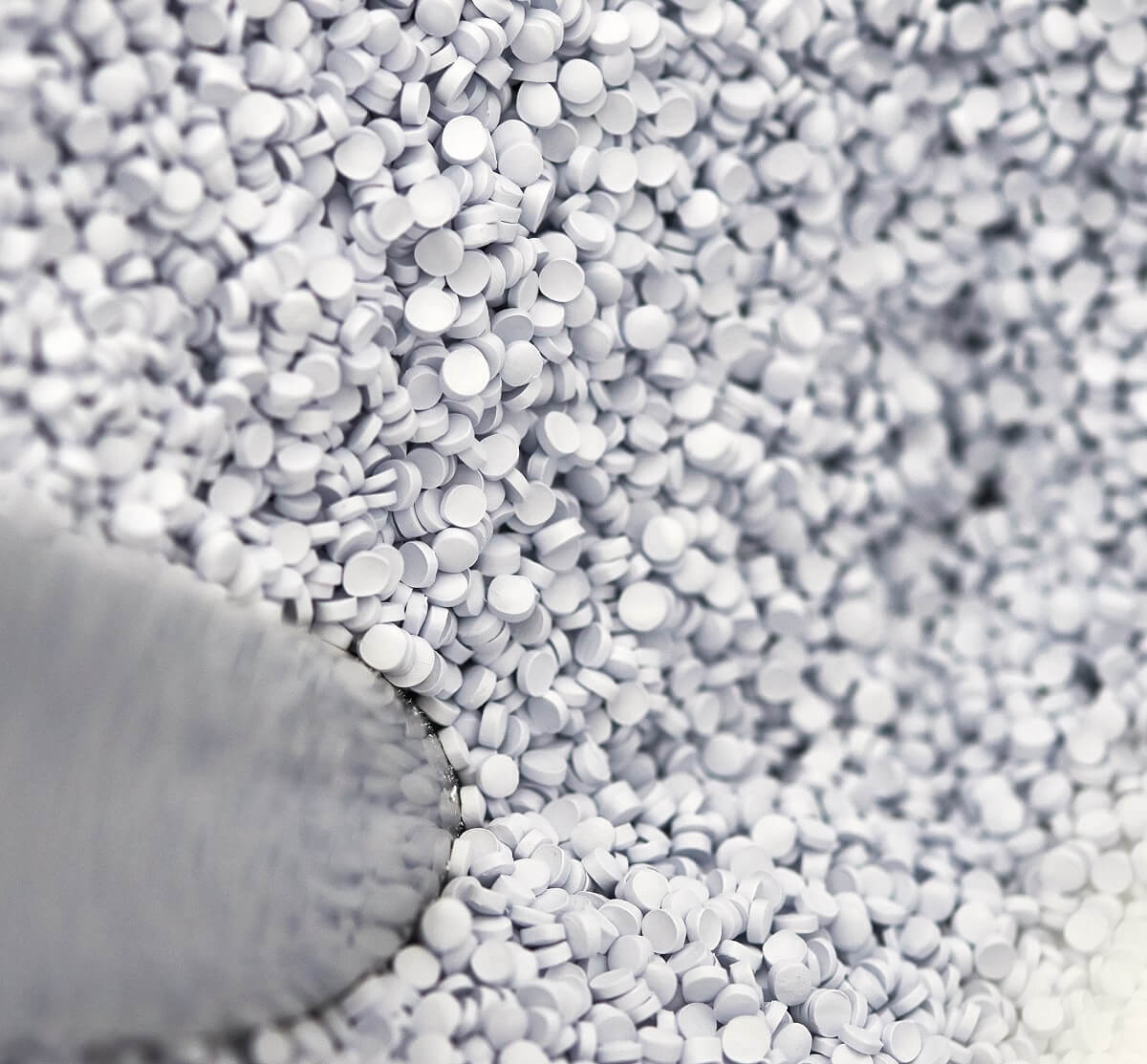
THE PVC
Well-known to professionals, PVC is a material that has no shortage of resources and is still very much in vogue: multi-purpose, resistant to external aggression (UV, precipitation, fire), non-oxidising, easy to maintain, decorative and with excellent insulating properties, it is also relatively easy to work and install as long as a number of basic rules are followed. PVC is 100% recyclable. The European industry has made considerable efforts to increase the collection of PVC waste and to optimise recycling technologies.
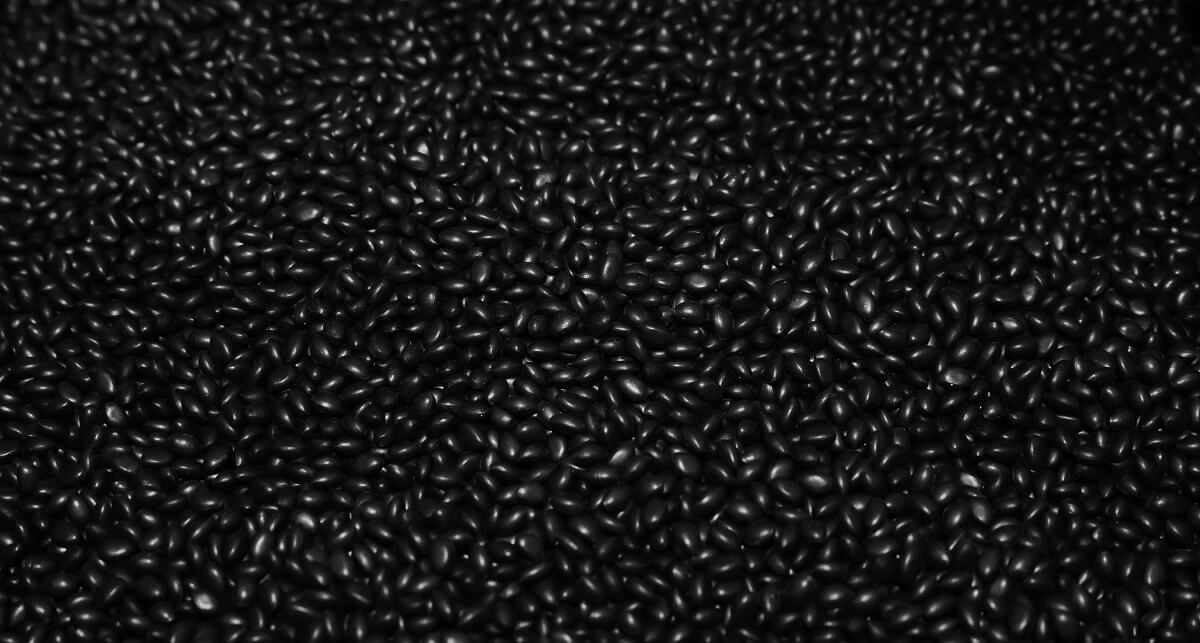
THE ABS
Acrylonitrile Butadiene Styrene, better known as ABS, is a thermoplastic widely used by Geplast, particularly in the manufacture of thermal breaks and aluminium joinery cores.
The material is used to manufacture rigid, lightweight, moulded products, and its primary quality is its resistance to impact at low temperatures (-40°C). ABS is also easy to recycle.