GEKO was born out of a desire to create a visual identity for all existing and future projects and products that are part of an “eco-design” approach.
Like a “gecko”, a type of lizard found in several parts of the world, the products in the range respond to three fundamentals :
- Eco-responsibility → nature
- Product quality → agility
- Customised solutions → great adaptability.
Since its creation in 2003, Geplast has been working to respond to these issues by offering innovative products that are part of a sustainable approach. Aware of the importance of reducing its environmental footprint for the good of the planet, Geplast makes maximum use of so-called “renewable” resources.
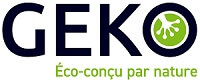
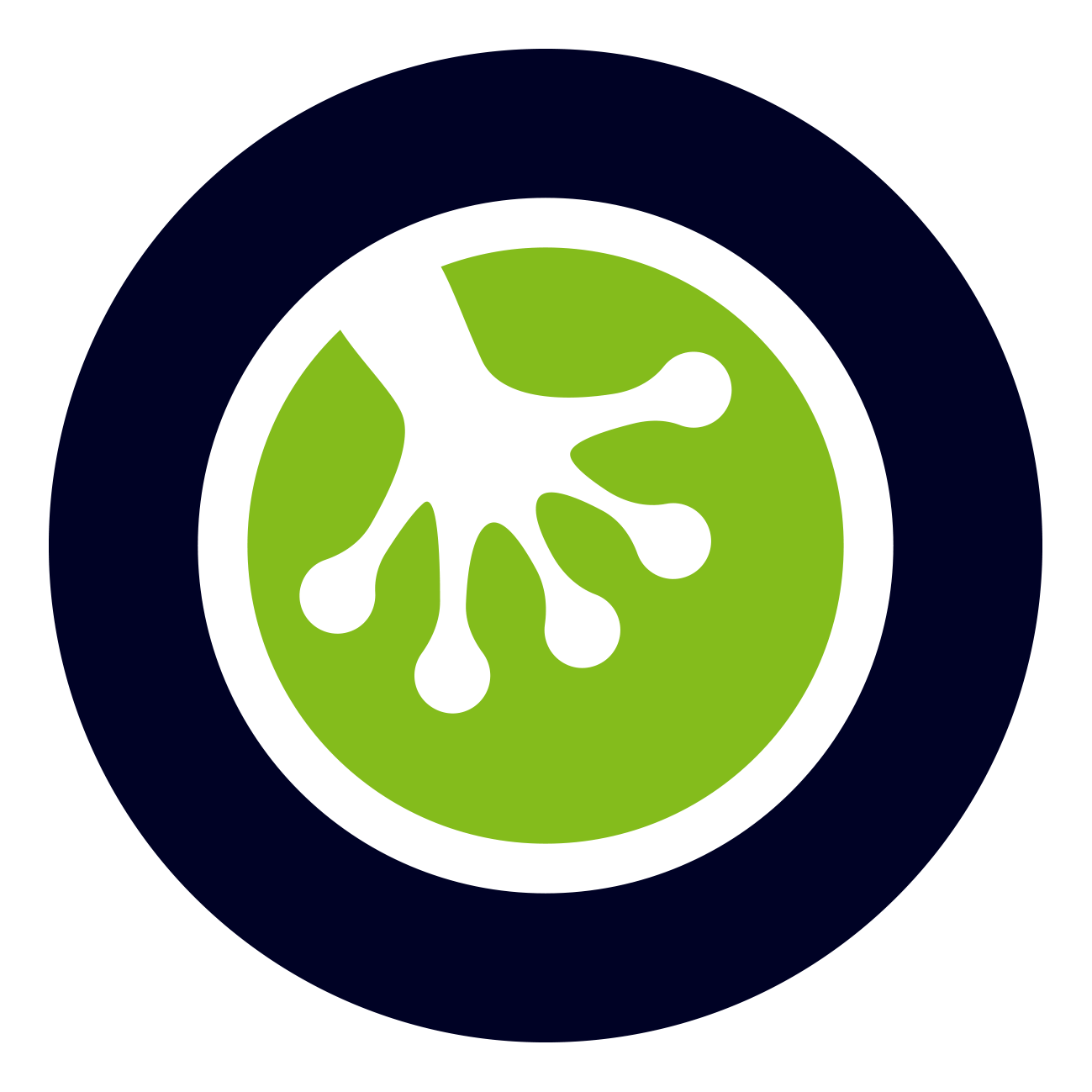
From the moment they are designed, GEKO products are part of a decarbonised and sustainable life cycle. As a matter of principle, and as far as possible, materials are never “raw”. All offcuts are sorted, crushed and re-extruded. At Geplast, by 2024, 40% of our processed materials will be recycled. In addition to recycled materials, GEKO also uses alternative composites, derived from virtually inexhaustible agricultural resources, and bio-sourced materials composed of 60% natural materials, such as rice husks, also known as Loryza®.
Since 2008, recycled material has been used as an undercoat for PVC cladding and joinery profiles. Today, 95% of angle sections, flats and flaps are made using co-extrusion. The proportion of recycled material in these products is over 80%, and is located on the non-visible part of the profile. Some of our other products are part of this approach: the IrYs box, designed using 98% recycled materials, and the new Oryzon collection from the Eclipse range, made from Loryza®.
Reducing our carbon footprint
The eco-design of our products also involves reducing our carbon impact. Since 2018, Geplast’s R&D department and EVEA have been calculating the carbon costs of our recycled materials and measuring the energy consumption of some of our extrusion lines in order to draw up Life Cycle Analyses (ACV) to produce Environmental and Health Declaration Sheets (FDES) for each product, which will be published in the Inies database and verified by regulatory bodies.
We then underwent an audit to prevent losses of GPI (Industrial Plastic Granulates) into the environment. Since 1 January 2022, all sites producing, handling and transporting industrial plastic granules must implement preventive measures to avoid losses and releases into the environment.
Following an audit by LNE, we obtained a certificate valid for 3 years. It demonstrates our approach to preventing GPI losses (from the arrival of the material to extrusion and recycling) and environmental risks in order to comply with the AGEC law (Anti-Waste and Circular Economy) decree n°2021_461.
All these actions fit in perfectly with our CSR approach and complement our GEKO brand. Our aim is to continue to innovate and reduce our environmental footprint.
Label MORE
For the fifth year in a row, Geplast has been awarded the first European label recognising our commitment to reducing the environmental footprint associated with the manufacture of our products by promoting the use of recycled raw materials.
Awarded by the French Plastics and Composites Federation (Fédération de la Plasturgie et des Composites), the MORE label (MO bilised to RE cycle) is proof of our progress in incorporating recycled materials into the production of our profiles.
Aware of the importance of reducing our carbon footprint for the sake of the planet, we are committed to using as many recycled materials and “renewable” resources as possible in the manufacture of our products.
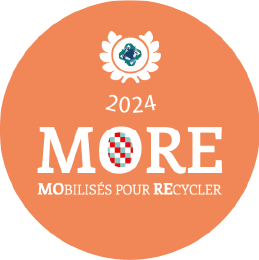
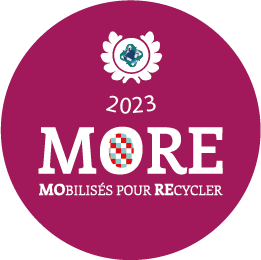
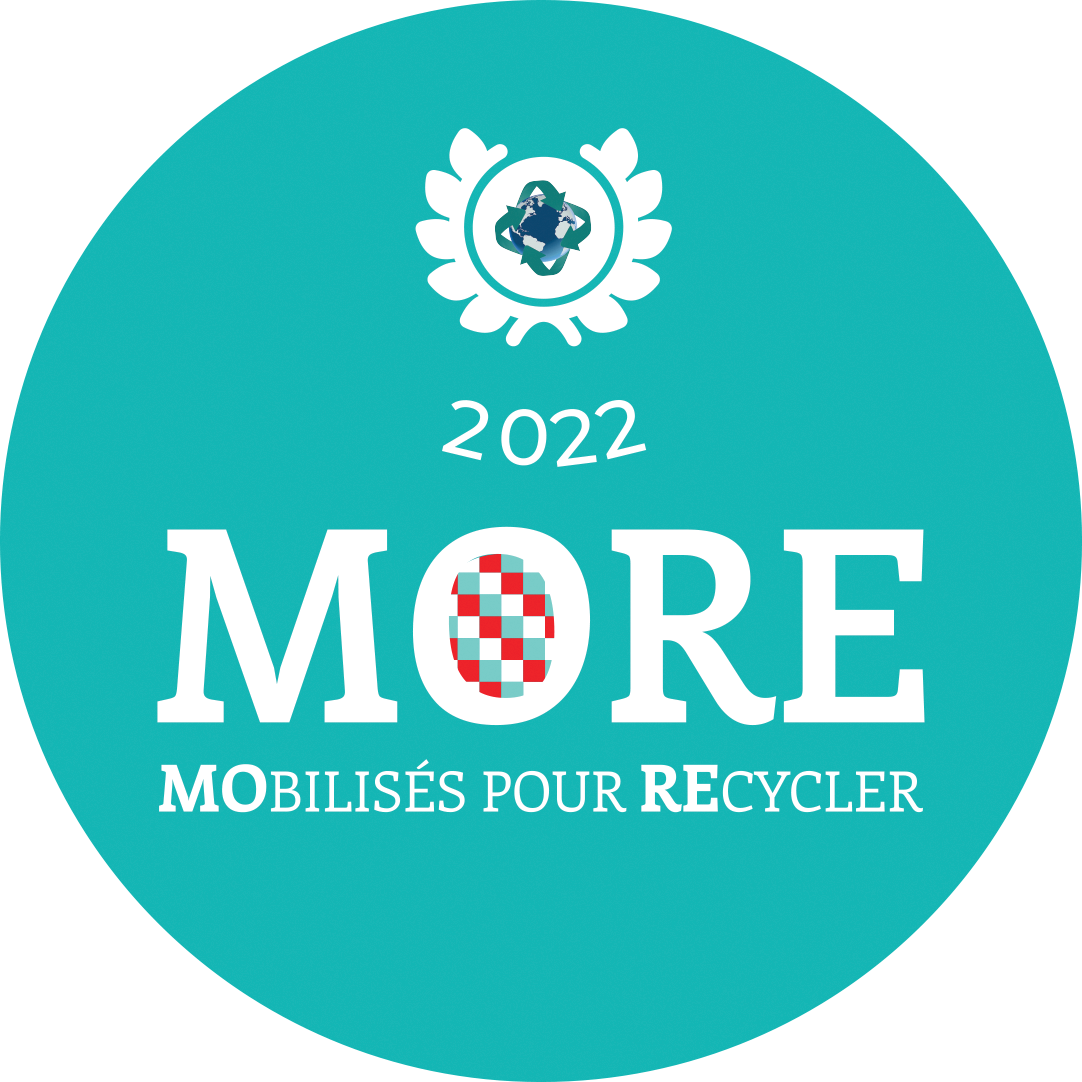
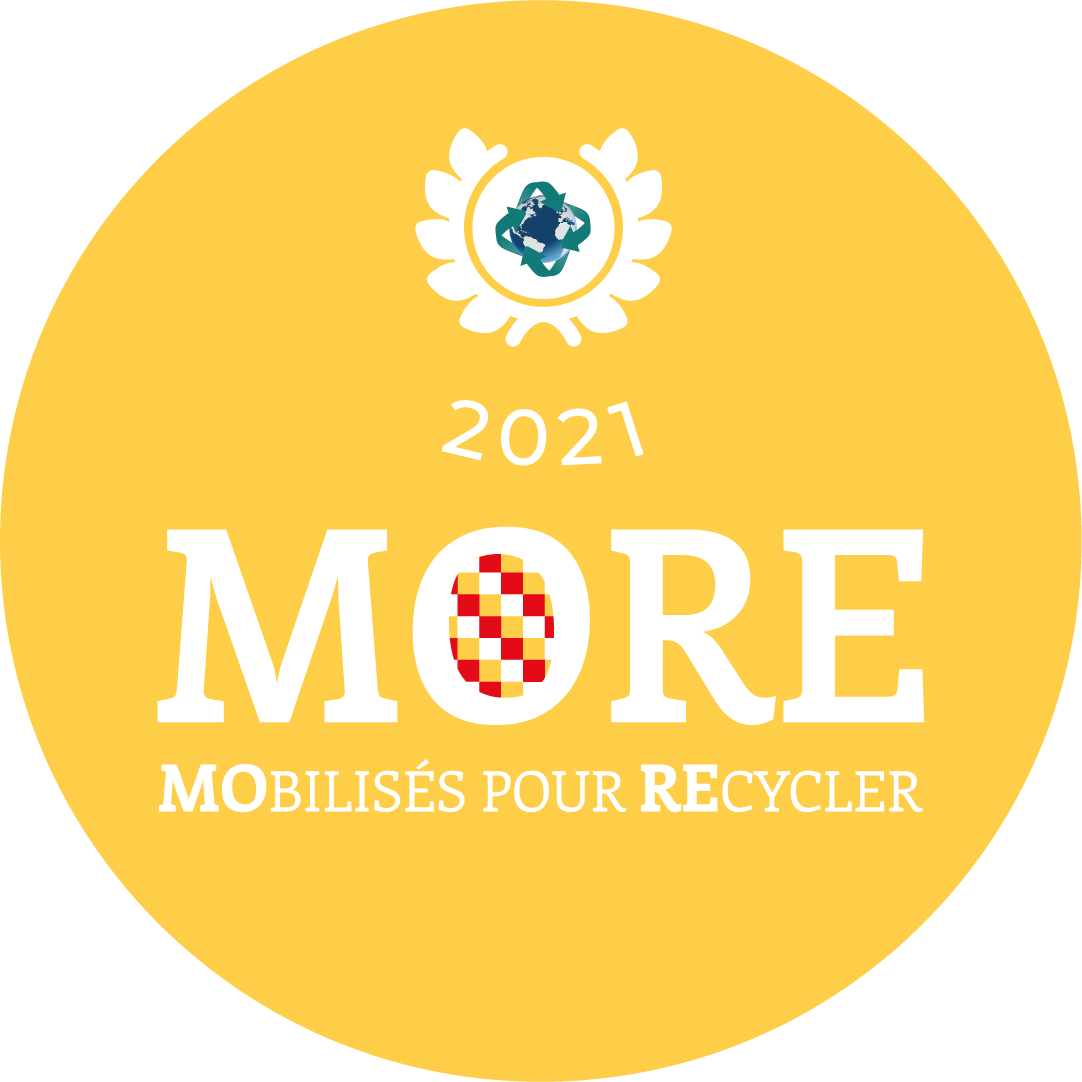
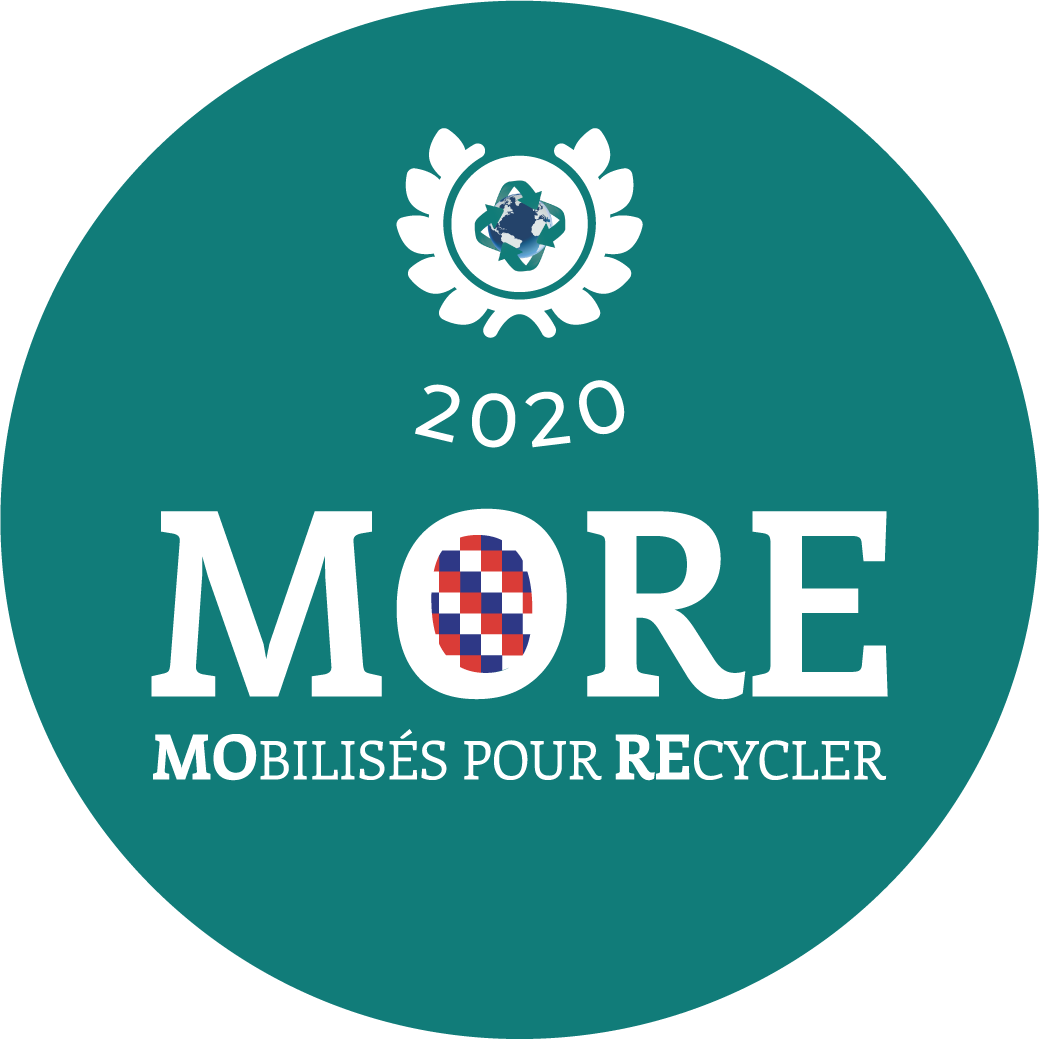